Irving Tissue Warehouse
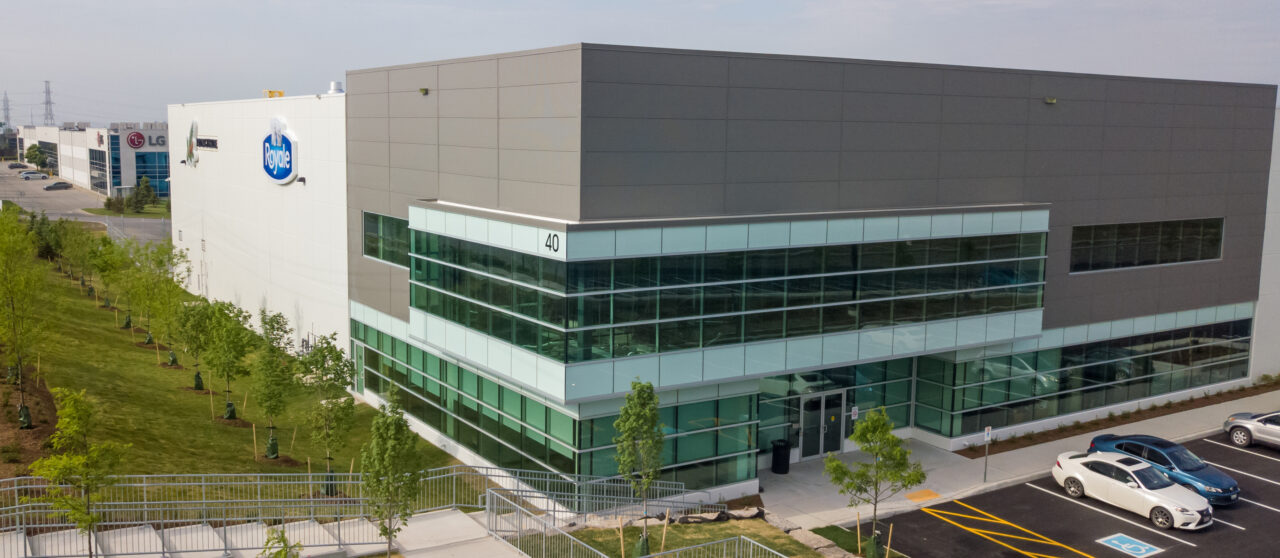
The Project
This LEED certified 150,000 sq. ft. industrial building is a secured facility with drive-in loading, sorting and distribution areas, vaults, and office space. Constructed of steel and delivered via design-build, this building has a bay size of 55’ X 40’. The building is insulated with precast concrete and metal panels. This project included the demolition of the existing communications utility building.
The Conversation Pieces
Situated right beside a major highway in Toronto, Ontario, this new building is home to a National supplier who asked for outdoor amenities and an aesthetics upgrade.
Painted precast and Aluminum panels were used to visually enhance the exterior of the building; significant elevation changes required various locations to be shored.
Project Specs
- LEED Certified
- Design-Build
- Drive-in loading, sorting and distribution areas, vaults, and office space
- Shoring and retaining wall systems used with terraces to support neighbouring heavy vehicle traffic
The Challenges
The main challenge was an existing utility building that was onsite. As well, a neighbouring property had a shared driveway aisle through the new site which needed to be relocated. The differences in the grades of the existing site plans in comparison to the revised ones required extensive use of retaining walls and shoring systems to support neighbouring buildings and heavy vehicle traffic.
The Solutions
To overcome the challenges, additional planning was required for the demolition and site preparation - mainly due to the specific function and design of the existing building. The robustness of the existing building was a significant schedule consideration as the existing foundations and surrounding soils were designed with the intention to withstand considerable seismic events. This impacted how Traugott was able to re-use large amounts of granular material and relocate native soils where it was required for the new building.
Traugott coordinated with many stakeholders including city planning groups and neighbouring lot owners. The addition of an access entry point through the adjacent property added time, however the project was delivered both on time and under budget.
Shoring and retaining wall systems were used with terraces to support neighbouring heavy vehicle traffic along with staffing amenity areas.